More sustainable thanks to new technologies
Efficiency at all levels - that's what we strive for in our production: whether it's the use of resources, the organisation of workplaces or the production routes travelled. We utilise innovations in production processes on our way to a more sustainable future by saving materials, energy or CO₂, for example.
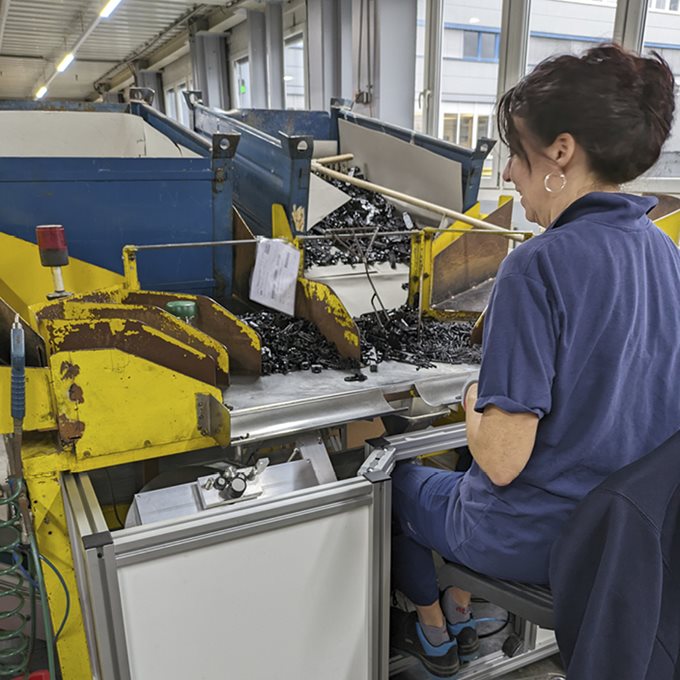
Optimise work processes
Designing workstations as efficient and ergonomic as possible - with this in mind, several departments are constantly scrutinised in 2023 and revised in terms of material flow, work safety and set-up times. The measures ranged from new lighting to the optimised feeding of materials and larger handling surfaces.
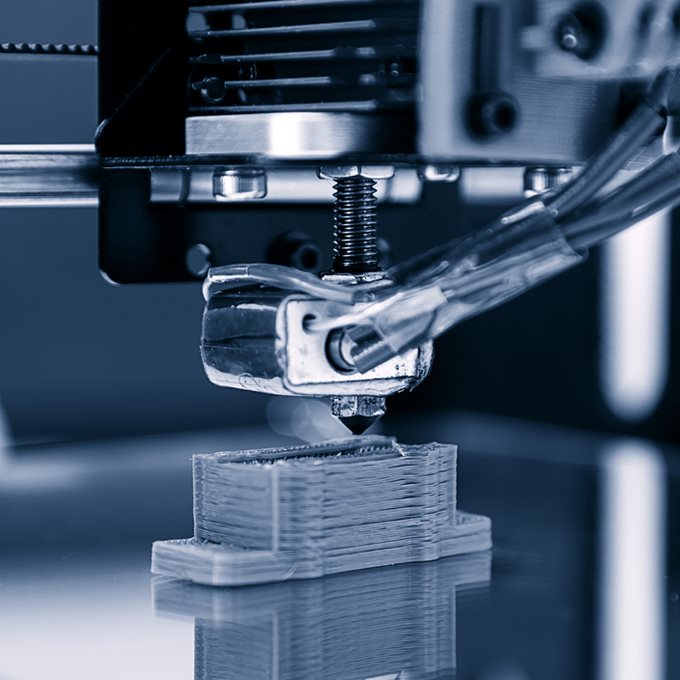
Small quantities in 3D
For batch sizes of less than 500 items, some items will be produced using the 3D printing process from the end of 2023. The flexible manufacturing process for very small quantities has the advantage that no extra tools need to be produced or machines converted. This saves material and energy and conserves valuable resources.
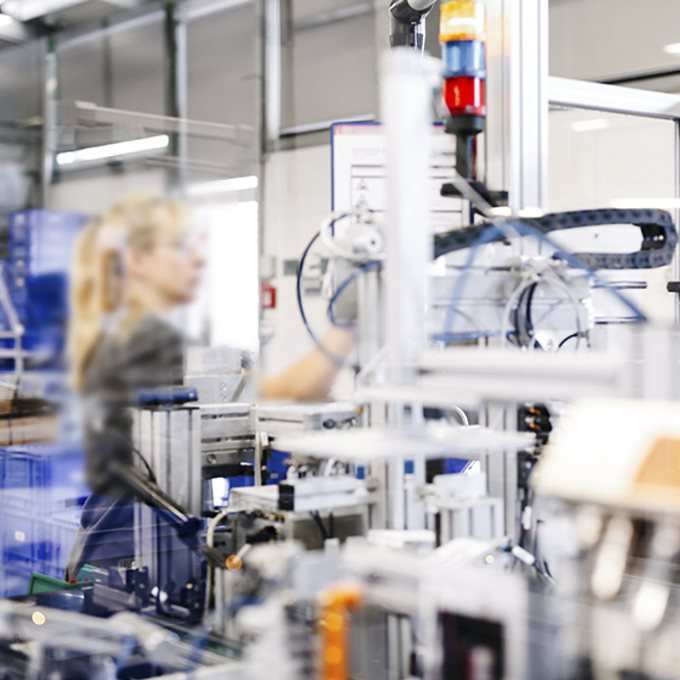
More efficient processes
At the Helpsen site in Germany, we have reorganised the production processes in order to significantly reduce internal transport between Plant 1 and Plant 2. In future, all materials will be produced in Plant 1 and then picked and packed directly in Plant 2. This saves time, reduces emissions and ensures that customers receive their deliveries even faster.
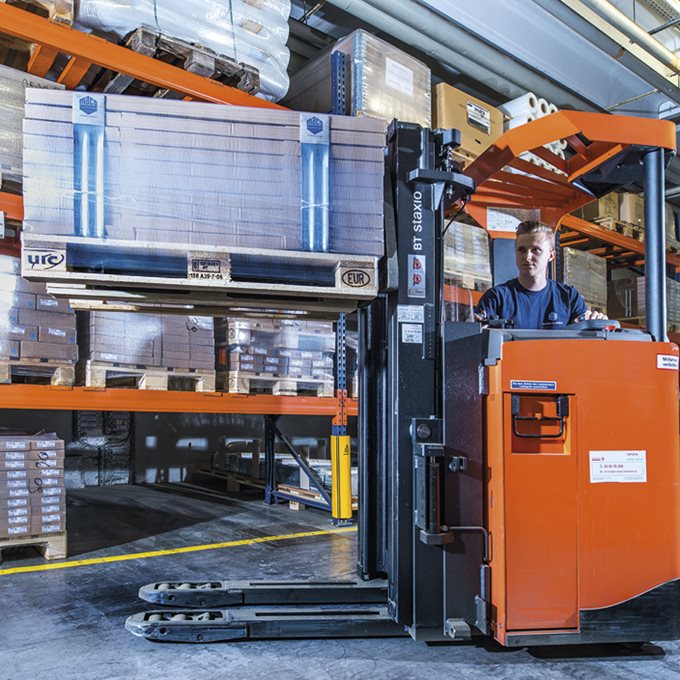
Shortening distances
Whether in an assembly area in Salzburg or in the warehouse, the distances that need to be travelled between individual work steps were significantly reduced in 2023 by rearranging and combining workstations. This reduced internal traffic - which also has an impact on occupational safety. The throughput time per item was reduced by almost half.
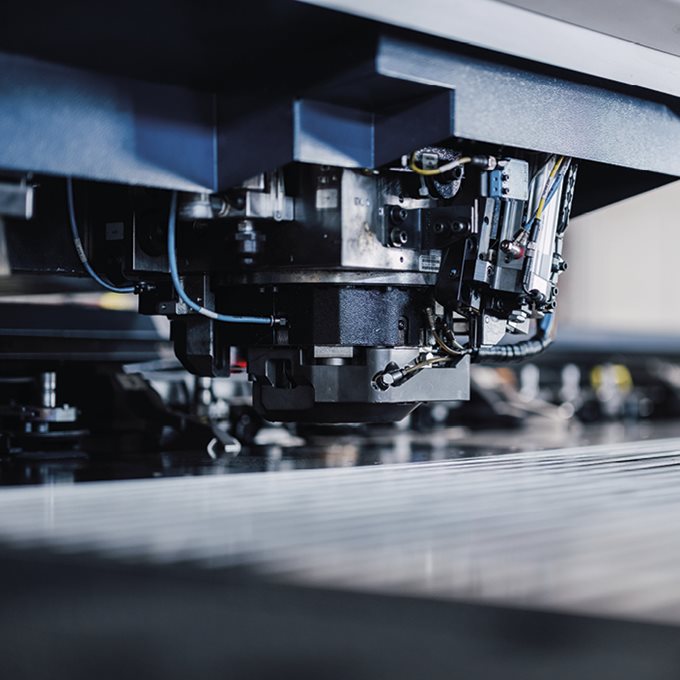
Renewing machinery
We are constantly optimising our machinery and replacing old production tools with new ones. Why is this ecological? The machines equipped with the latest technology require less energy, work more efficiently, generate fewer rejects and emit less CO₂.
We invest several million euros a year in our machinery - and therefore also in the environment.
Using existing technologies more efficiently
Increasing not only the efficiency but also the longevity of our production facilities - this was the aim of several projects in 2023 and 2024. An excerpt.
Regular maintenance prevents premature wear and loss of quality - regardless of whether this involves machinery, the vehicle fleet, protective clothing or the maintenance of production sites, to name just a few examples.
MACO has several tools in use that focus on specific areas of application. They report when services and inspections are due. This allows each branch to maintain an overview and take countermeasures in good time if necessary.
In 2023, MACO UK implemented its own management tool tailored to the branch. Over 100 different positions are mapped here.
How does the tool sound when punching? A change in the sound allows conclusions to be drawn about its condition: this allows you to recognise at an early stage whether there is a defect or something needs to be replaced. We therefore rely on ultrasonic sensors that monitor the sound of our punches, report deviations and enable maintenance to be carried out as required.
Not only do tools remain in use reliably for a long time, we also prevent premature wear of the entire system and extend its service life.
We are proud of our in-house production rate of 95 per cent. We also manufacture most of our tools ourselves. However, there are frequent downtimes when installing and adjusting the tools in the series machines.
To reduce such downtimes, we set up the technical centre in Salzburg in 2023. In the specially created room with a test press, we develop tools, but can also maintain and improve them at our leisure and use them to produce initial sample parts. Only when the tool is fully customised will it go into series production.
This enables us to reduce tool wear and error rates, make series production more efficient and speed up tool development. It also improves our material efficiency.